As winner of numerous international awards, Bruschi Spa is known for its innovative approach in design and technology. We are glad to share our insights and experiences with the industry members.
Focus on Surface Finishing
In this post we are going to describe what is meant with surface finishing and we will explain why it is important to take them in consideration from the designing phase of a component, giving some advice for the optimization of the most critical points.
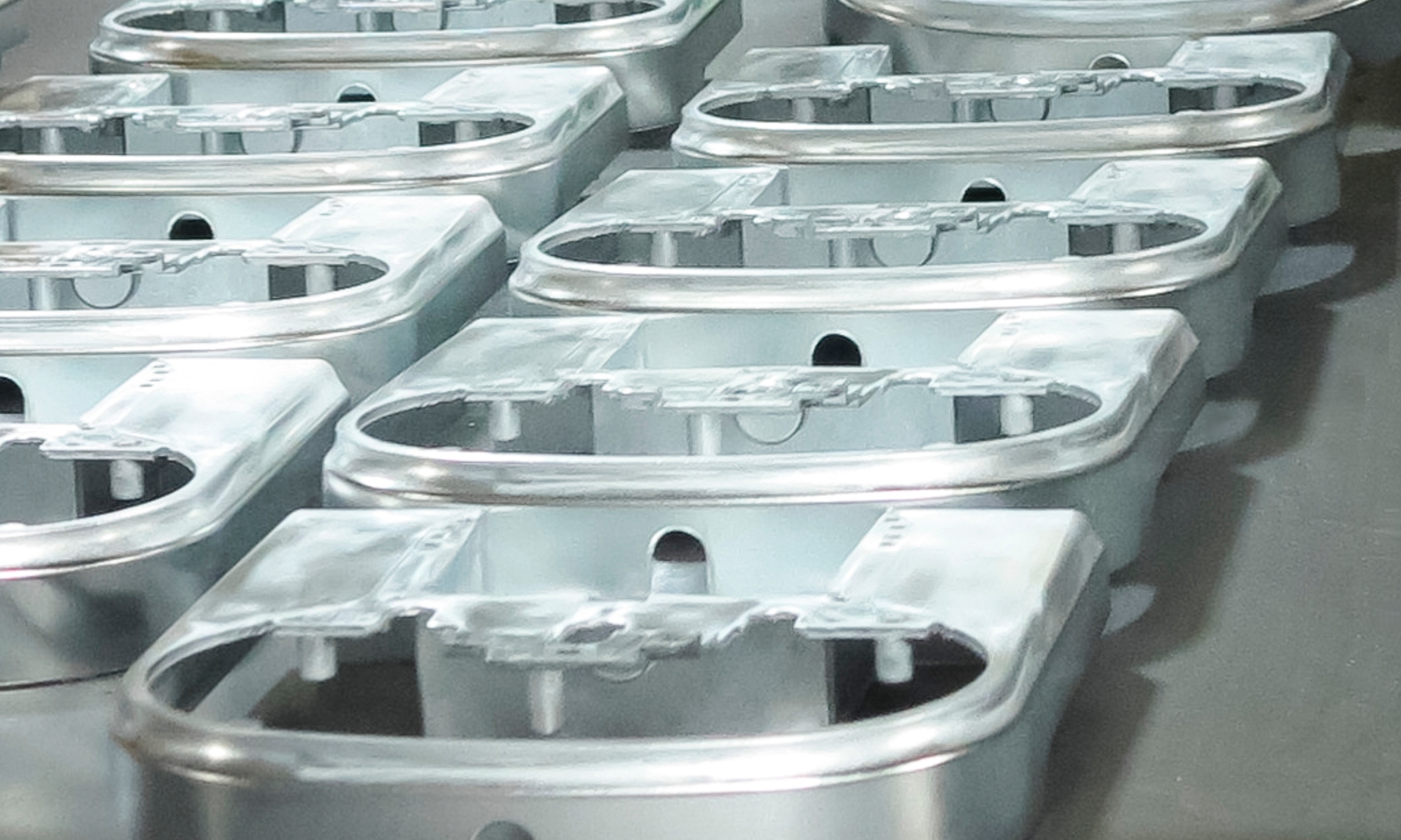
First of all, it is important to point out that surface finish is different from surface finishing: the first refers to the texture of a surface, for example whether it feels smooth or rough at the touch, while the second one identifies all the industrial processes aimed at changing the surface texture.
Surface finishing include a wide range of industrial processes that can modify the surface of a manufactured item, product or component to reach and improve a property or a characteristic. Except for components made of noble metals, almost all metal parts need finishing after manufacturing. Different finishes can be chosen for different reasons: to improve the appearance of a product, to enhance chemical resistance, corrosion resistance or wear resistance, to improve or modify electrical conductivity, to remove burrs and other flaws and to modify surface texture.
Sometimes more than one of treatment can be applied at the same time, for functional or aesthetic reasons: for example, in order to achieve the best result, aesthetical treatments like chroming or varnishing are usually preceded by special treatments to prepare surface. There are different kinds of processing techniques: some can be used as a last step of finishing while others are used to prepare surface for secondary surface treatments. The choice of treatment depends on product design and on client’s requirements. Thanks to these kind of treatments, it is possible to prevent surface defects caused by external agents, that could damage the product.
Another reason to apply surface finishes is to improve a part functionality: for example, machining processes are used not only to smooth out sharp edges, but they can also increase roughness to grant a better grip on handles and similar components.
As stated before, most metals products requires finishing processes: the majority of aluminum, magnesium and zinc die castings will receive at least one post-casting finishing, depending on specifications of durability, protection and aesthetic requirements.
One of the most common processing used in die casting is deburring: burrs are extremely common and they constitutes a cutting hazard because of their sharpness. There are different techniques to remove burrs, from hand-made deburring to thermal deburring, done with specific machines. Deburring is often followed by a conversion coating to remove any remaining oil, die-cast release agents and other contaminants.
The conversion coating process consists in creating a coating on the surface of a metal part by making the surface react with a chemical. This coating is mostly used as preparation and primer for the final painting, but in some cases, it can be used as final finish: especially for functional components that will not be seen after assembly, the use of only one finishing can grant cost savings.
Nevertheless, sometimes strictly functional components can require more than one treatment too: when there are strict functional specifications, such as corrosion protection and heat dissipation, it is recommended to use a combination of conversion coating and functional coating to meet clients’ requirements.
To achieve the best result and avoid discovering after casting that a component is not suitable for a certain treatment, it is advisable to consult a supplier already in product design phase, as we will see in the next part.
THE IMPORTANCE OF COLLABORATION FOR SURFACE TREATMENTS
Today’s technology allows to obtain die casting products with excellent surface finishes. To achieve the best results and manage costs, it is essential to know in advance every process that should be applied to the product.
Applying surface finishing to die cast products involves multiple variables: forecasting eventual problems and finding solutions makes it possible to improve manufacturing time and increase saving, guaranteeing requested quality.
In manufacturing terms, products are defined by precise specifications and surface finish depends on functional or aesthetic requirements. Even if the most relevant aspect of product design is the final purpose of a component, it should be taken in account that treatments result can be influenced by shapes or geometry of products, and even cause surface defects.
For this reason the collaboration between costumers and supplier should be constant in every phase of product development through a co-design activity, in order to spot critical shapes and obtain a simpler and more defined process. This allows, for example, carrying out proper modifications of critical surfaces, edges and mounting features, to obtain components that require minimum surface preparation prior to application of a final coating. Design modifications are not always possible but, if feasible, they can lead to consistent enhancement in surface finishes quality.
As said before, it could be advisable to plan post-casting finishing process during design phase. In fact, design features impact directly on achieving particular surface finish: for example, the presence of hollows on the component could cause lacks of painting. To know more about painting defects, click this link.
A partnership between casting supplier and its customer can thus improve not only post-casting processing, but also final functional or aesthetical surface treatments, such as painting or galvanic treatment.
SOME SUGGESTIONS ON HOW TO OBTAIN A BETTER OUTCOME
As said above, there a few precautions that can help obtain better finishing results. Here are a few pieces of advice that can be applied before casting to obtain concrete advantages in terms of product design and finishing. It is a list of suggestions that can simplify processes, cutting extra costs during production phase and finishing.
Parting lines
Parting lines are one of the unavoidable consequences of die casting: where the two halves of the mold meet, a parting line will be formed. An early consultation with supplier on aesthetic features assures proper placement of necessary parting lines, to conceal trimmed visible edges and eliminate the need for post-casting edge polishing.
Countersinks
To assure integrity of tapped holes’ surface edge, leading threads can be protected from deburring or polishing with countersinks or counterbores placed on die cast holes for machining.
Wall thickness
Where needed and feasible, wall thickness can be created on bosses to avoid scuffing on surrounding painted surface areas.
Ribs
Well-designed ribs improve die fill and avoid resulting sink marks on surfaces. Short and stocky bosses optimize metal flow and insure integrity of the feature.
Radius
Using the maximum allowable radius for all internal and external corners improves cavity filling and makes it possible to reach all part’s surfaces with vibratory deburring equipment.
Housings
A good design of housings diecast corners can also assure complete filling of the die cavity and corners integrity.
Cast-in textured surfaces
During die construction cast-in textured surfaces can be produced on selected areas of a component by special preparation of the die.
These are just a few of the most common suggestions to improve the final outcome of surface finishing process and to reduce wastes during die casting, but an experienced supplier will be certainly capable of suggesting the most fitting solution for each product. Since there are multiple variables to consider related to a specific product, it would be impossible to make general suggestions applicable to all circumstances, for each case deserves deep attention.
To have further information on die casting and always be up-to-date with the industry, subscribe to our blog.