As winner of numerous international awards, Bruschi Spa is known for its innovative approach in design and technology. We are glad to share our insights and experiences with the industry members.
How to avoid defects in die casting surface treatments: painting and varnish
In this post we are going to analyze some surface defects in die casting linked to errors in the painting process of zinc die cast products.
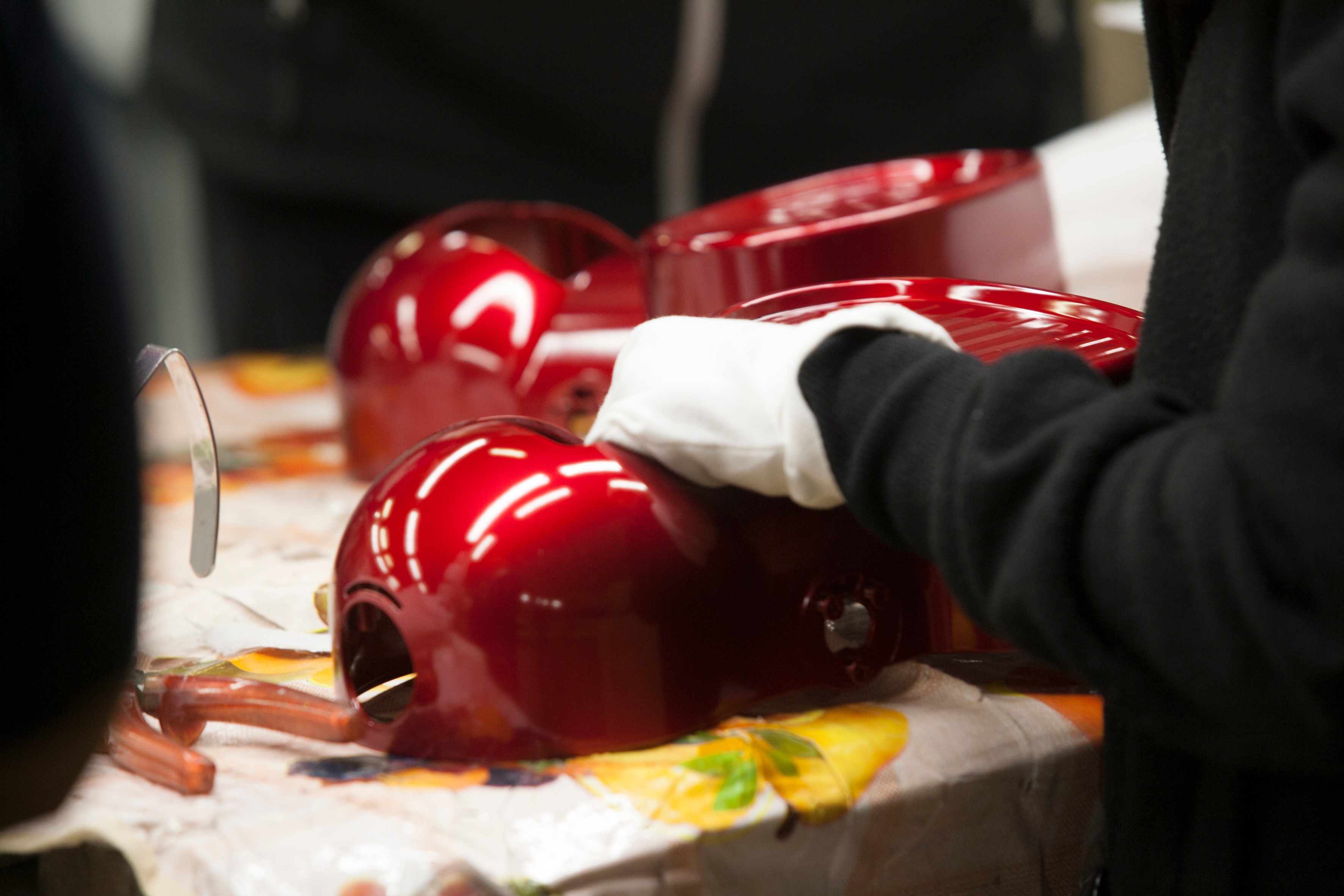
When products require a high aesthetic impact, painting is often the best choice thanks to its versatility: not only does it offer a wide variety of colors, but it also determines the final texture of the product. Different painting processes make it possible to achieve matt textures, shiny textures and even metallic textures at a lower price than galvanization. Moreover, painted products gain extra surface resistance thanks to additional layers and to passivating treatments preceding coating.
However, like every industrial process, there are many factors that can compromise the final result. When working with die casting, some errors are more common than others. For example:
- Hue variation
- Fizzing
- Blisters
- Deformation
- Peeling
- Lack of paint
- Pitting
- Thin or scarce layer
- Orange peel
Now we are going to describe these defects, along with their causes and how to prevent them.
Hue variation
Hue variations can affect a single component, which could present different colors in some areas or darker shades, but they can also affect different batches of the same product, so that the first batch would be of a different hue than the followings.
These discoloring can be caused by expired or poorly stored powder, by fumes blackening some parts of the product, by variations in temperature or in baking time between each batch.
During painting, components are heated up to ease the application of powder painting and could be exposed to UVA rays or heated up again, depending on the treatment and the required finishing. Because of this, it is fundamental that time and temperature set for the first batch are exactly the same as the following batches and that they aren’t changed during the production. In addition, temperature control should be performed with carefully calibrated pyrometers.
Fizzing
Fizzing appears like small bubbles, very similar to blisters but smaller in dimensions. They are usually in groups and sometimes bubbles can have a central hole. In most cases they are caused by water or solvents trapped in porosities on the piece surface and emerged after heating.
These trappings can be avoided by carefully cleaning and drying the components, for example by pre-heating them up to 100°C or by using warm air instead of steam to dry them.
Blister
Blisters look like bubbles adhering on the metal surface, usually not bigger than 8 mm. Generally, blisters aren’t properly a defect in painting, but defects in die casting caused by air trappings and porosity laying under the surface that emerged after component’s heating.
In order to avoid this problem, it is possible to improve the distribution of porosity in casting through the use of a simulation and to test each component by pre-heating it before moving on with the painting phase. As an alternative, it is possible to reduce baking time and use the lowest temperature possible to avoid blisters from emerging.
Deformation
This kind of defect is rarer than the previous one, but it is still important to know how to identify it: it occurs when a component can’t bear the heat and creeps after baking, or when painting supports apply an excessive strength on the component, deforming it. It can be caused by some defects in die casting process or by a bad design.
To avoid this problem, it is advisable not to use high temperatures and to check positioning on the hangers and strength applied by supports. In some cases it could be necessary to modify the product design: asking suggestions to a trustworthy supplier would be advisable, to make sure that the design is suitable for the chosen industrial processes. This may sound like a simple advice, but it can prevent further complications and improve the overall functionality of the component.
Peeling
Peeling are areas in which the paint coating was applied unevenly or is easily removable. This usually happens due to surface contamination caused by oils, fats, oxides, powders but also fingerprints. It is an easily avoidable problem: a careful cleaning and the use of gloves to manipulate each component should be enough to prevent the formation of this defect.
Lack of paint
This defect is typical of electrostatic powder painting: with this particular technique, an electric field is generated between the tip of the painting gun and the component. Normally this helps powder paint to stick to the surface evenly, but when a component has sockets, hollows or ducts on the surface, a Faraday Cage could form and make the electric field head toward low resistivity zones, such as channels edges, dragging along powder painting particles. As a result, there will be heaps of paint on the borders of the hollow, and a lack of it on the internal surface.
To avoid these situations and make sure that varnish may reach the inside of hollows, it is advisable to reduce painting gun voltage: as a consequence, strength of the electric field near the component surface will decrease too, improving penetration rate of particles through Faraday cage by weakening the force pulling particles towards hollows’ borders.
When designing a component destined to electrostatic powder painting, it is advisable to avoid deep hollows and steep curves, to prevent the Faraday cage effect.
Pitting
Pitting looks like small granules underlying paint coating. They usually appear in groups and are caused by presence of dust on the component. To avoid their formation it is necessary to assure a meticulous cleaning of both working environment and components, even in storage phases, by cleaning them with electrostatic cloth or with compressed air.
Thin or scarce layer
The expression identifies those zones in which the paint coating is transparent or inadequate, which are usually located near the edges of a component. They can be caused by scarce quantity, linked to a low powder dosage, or by wrong spraying parameters, unsuited for the component shape.
In addition, there could be problems with grounding that cause interferences between electric field, preventing the correct sticking process. For all of these cases, the solution is controlling and correcting process parameters and defects.
Orange peel
As the name suggests, this defect makes the painted component surface similar to orange peel: instead of being polished and smooth, it displays small bulges that makes it feel rough to the touch. It is a defect caused by excessive thickness of the painting layers: in order to prevent it, it is necessary to check the correct operation of nozzles and their positioning, and to modify system settings to spray a thinner layer.
To sum up, we have listed the most common defects in die casting painting processes, analyzing for each of them the root cause and explaining how to prevent them. To avoid this kind of defects, the best solution is to relay on expert and trusted suppliers, capable of suggesting the best kind of pre-finishing for the desired painting process.
To always be up-to-date with die casting news or to read more on how to avoid defects in die casting, subscribe to our blog.
